Building the Future: The Rise of Modular Construction

In the rapidly evolving world of construction, modular construction has emerged as a game-changing innovation. Rooted in the concept of assembling prefabricated building components off-site and transporting them for final assembly, modular construction is transforming how we design, build, and think about spaces.
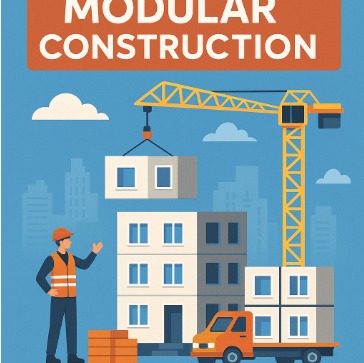
The Present Landscape
Modular construction is not a novel concept, but recent technological advances and market demands have significantly accelerated its adoption. Today, hospitals, hotels, schools, offices, and even high-rise apartments are being built using modular methods. Countries like the United States, the United Kingdom, China, and parts of Scandinavia are at the forefront, driven by the need for faster, more efficient building solutions.
Several high-profile projects have brought modular construction into the spotlight. For instance, in London, a 44-story residential tower, “Apex House,” was built in record time using modular techniques. In China, entire hospitals were constructed within weeks during the COVID-19 pandemic, showcasing modular construction’s ability to meet urgent needs swiftly and effectively.
The growing popularity of Building Information Modeling (BIM), 3D printing, and automated manufacturing has further fueled this trend, enabling precision in design, reducing errors, and improving coordination among teams.
Advantages of Modular Construction
One of the most compelling benefits of modular construction is speed. By fabricating modules concurrently with site work, construction timelines are drastically reduced—often by 30% to 50% compared to traditional methods. This efficiency also translates into cost savings, especially in projects where delays can be financially devastating.
Quality control is another significant advantage. Modules are built in controlled factory environments, minimizing exposure to weather and ensuring consistent construction standards. This environment also supports safer working conditions, with fewer hazards compared to on-site construction.
Sustainability is a driving factor as well. Modular construction produces less waste, requires fewer on-site deliveries, and allows for easier recycling of materials. Some modular buildings are even designed for disassembly and reuse, aligning with principles of the circular economy.
Additionally, modular construction allows for better scalability. Developers can replicate and adapt modules to meet varying demands across regions, making it ideal for expanding housing or infrastructure in underserved areas.
Challenges and Limitations
Despite its promise, modular construction is not without challenges. The upfront investment in factories, design systems, and logistics can be significant. For developers used to traditional methods, the shift in processes and planning can be daunting.
Transportation is another hurdle. Large modules must be transported from factories to sites, often requiring special permits and routes. In urban environments, this can be particularly complex.
Design limitations also exist. While modular systems are becoming more flexible, early-stage projects often faced criticism for being boxy or lacking architectural diversity. Creative architects and engineers are now pushing boundaries, but perceptions persist.
Another barrier is regulatory complexity. Building codes and zoning laws often lag behind innovation. In many regions, approval processes are not yet adapted to the unique aspects of modular construction, causing delays and adding costs.
Finally, skilled labor shortages in factory-based construction pose a risk. As demand grows, the industry must develop training programs and career pathways to support this shift in workforce needs.
The Future Outlook
The future of modular construction looks promising, shaped by digital innovation, urbanization, and environmental urgency. Integration with smart technologies, such as the Internet of Things (IoT), robotics, and artificial intelligence, will streamline factory production and enhance building performance. Real-time data analytics could improve everything from energy efficiency to maintenance.
Sustainability will remain a key driver. As cities push toward net-zero goals, modular construction’s efficiency and adaptability make it a vital tool. Hybrid approaches—combining modular methods with on-site customization—are also gaining popularity, offering a balance between standardization and uniqueness.
Furthermore, the trend of “design for manufacturing and assembly” (DfMA) is being embraced, encouraging architects and engineers to work closely with manufacturers from the earliest stages. This shift could lead to entirely new forms of architecture that prioritize efficiency and innovation.
Global expansion is expected as well. In developing countries, modular construction could help address housing shortages and disaster relief needs quickly and affordably. Governments and international organizations are starting to recognize its potential in improving infrastructure and public services.
Conclusion
Modular construction is more than a trend—it’s a transformative approach to how we build in the 21st century. With its promise of speed, sustainability, and scalability, it is uniquely positioned to meet the world’s growing demand for smarter, faster, and greener construction. Though challenges remain, ongoing innovation, investment, and collaboration will likely cement modular construction as a cornerstone of the built environment in the decades to come.